The 4 Pillars of our Supply Chain Strategy
We prioritize anticipation, flexibility, responsiveness, and flow optimization to deliver a fully integrated Supply Chain strategy.
Anticipating & mitigating risks
Resource optimization via a shared ERP (SAP), lean management and proactive risk management.
Ensuring maximum flexibility
Build up safety stocks of the most critical components. Activate levers to increase our production capacity from one week to the next
Enhancing responsiveness
Use of predictive models (AI) to adjust our organization, tools and processes to market changes.
Optimizing flow management
Optimized stock management thanks to automation, traceability, customized logistics, and secure storage solutions.
Anticipating and Mitigating Supply Risks
We integrate forecasts and orders in real time, and simulate their feasibility on the basis of component availability and production capacity. Thanks to Lean management and our privileged relationships with our suppliers, procurement and manufacturing cycle times are reduced.
Our scope includes:
- Monitoring component lead times
- Monitoring of MOQ (Minimum Order Quantity) and stock coverage generated to limit the risk of excess and obsolete stock
- Risk analysis tailored to your project
- A dedicated crisis unit for sourcing critical components,
- Zero tolerance for counterfeit parts.
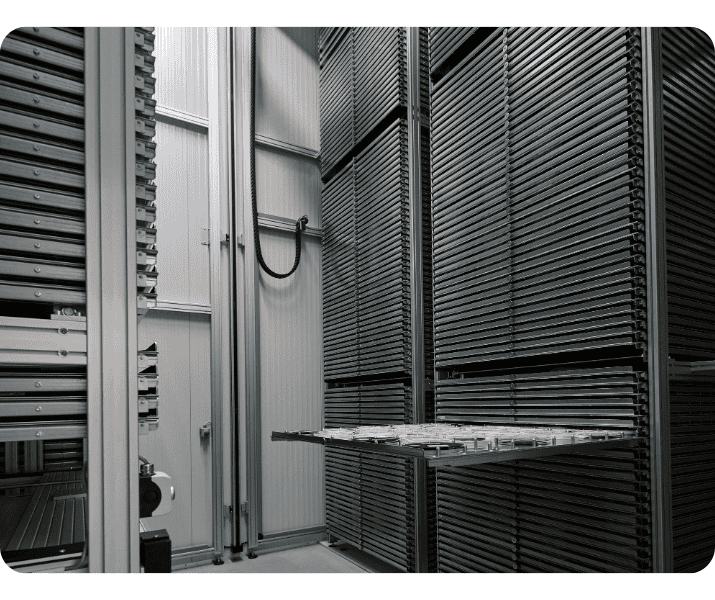
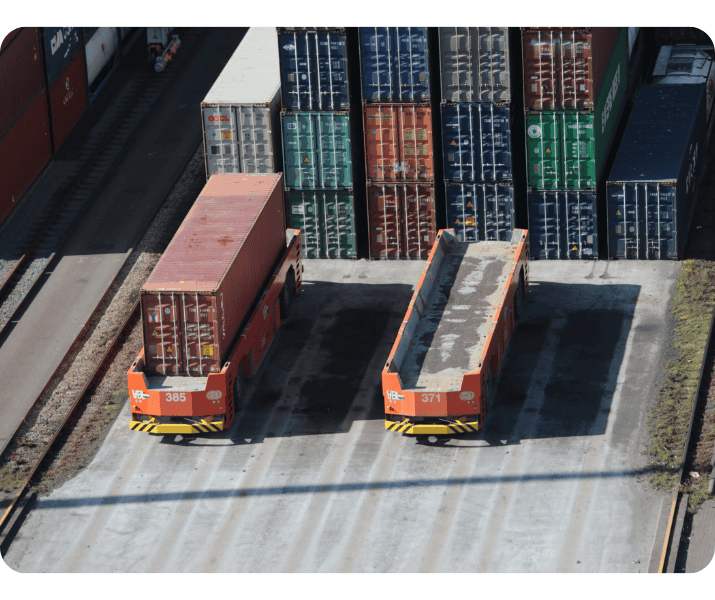
Ensuring Maximum Flexibility
Market conditions can be unpredictable, which is why we guarantee high flexibility, including:
- A Material Requirements Planning (MRP) strategy: make-to-order, make-to-stock, late differentiation
- Secure just-in-time supply chain management
- Bottleneck and subcontractor management
- Advanced workload management solutions, considering operator skill sets
- Finished goods and raw material inventory management under various models: Vendor Managed Inventory (VMI), Customer Managed Inventory (CMI),
- Kanban implementation at all levels of the supply chain.
Enhancing responsiveness
A strong Time-to-Market strategy requires rapid responsiveness, ensuring fast delivery commitments based on material availability and production capacity. To achieve this, we use:
- An integrated ERP, instantly assessing capacity and material constraints across production sites,
- An ERP connected to real-time market component availability for instant procurement of critical parts,
- EDI and Web EDI for seamless data exchange,
- A customer portal for real-time visibility,
- Advanced analytics tools to collect and analyze Supply Chain data.
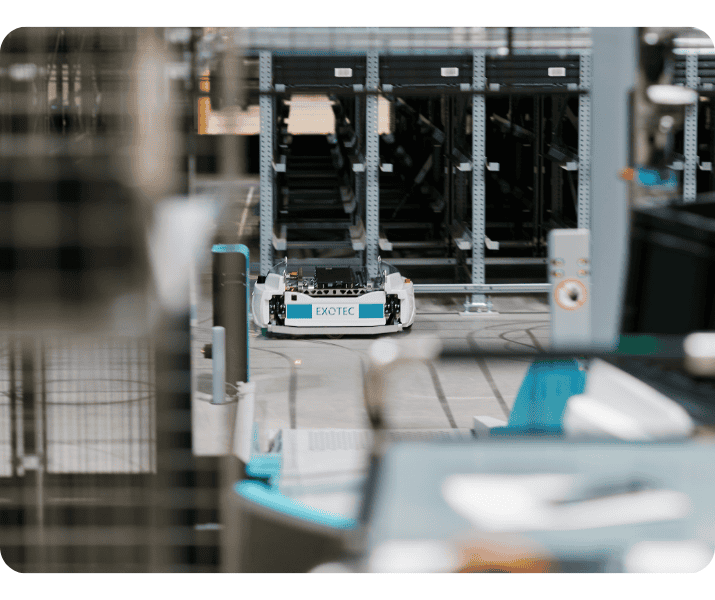
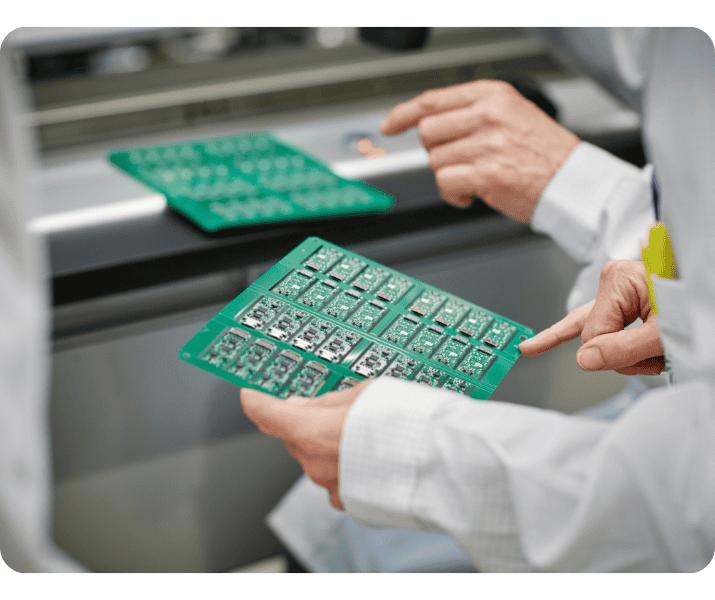
Optimizing Flow Management
To address financial and environmental concerns, we offer:
- Custom solutions for labeling, packaging, and logistics.
- Advanced warehouse management, including camera-based receipt scanning, X-ray counting, cobots, AGVs, and Track & Trace.
- Global logistics expertise and specialized storage for moisture-sensitive components, secure zones, and ROHS compliance.
Take control of your supply chain with an agile & efficient approach
Optimize your logistics and secure your supply chain with our expertise. We offer tailored solutions for enhanced flexibility, risk anticipation, and optimized flow management. Boost your responsiveness and efficiency with advanced management tools and dedicated support.