Our end-to-end offer for Industry,
from Design to Manufacturing
We provide innovative, connected solutions that optimize performance, promote digital transformation and guarantee seamless integration and scalability for intelligent industry.
Optimized
TCO
We minimize costs with efficient resource management & long-term optimization
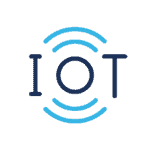
Dedicated
IIoT offer
Our generic IIoT platforms facilitate the development of your connected object projects
Time-to-Market Time-to-Volume
We accelerate the development and industrialization of your projects, whether in small or large production runs
Lean
Management
We improve processes to enhance efficiency, reduce waste, and ensure high quality
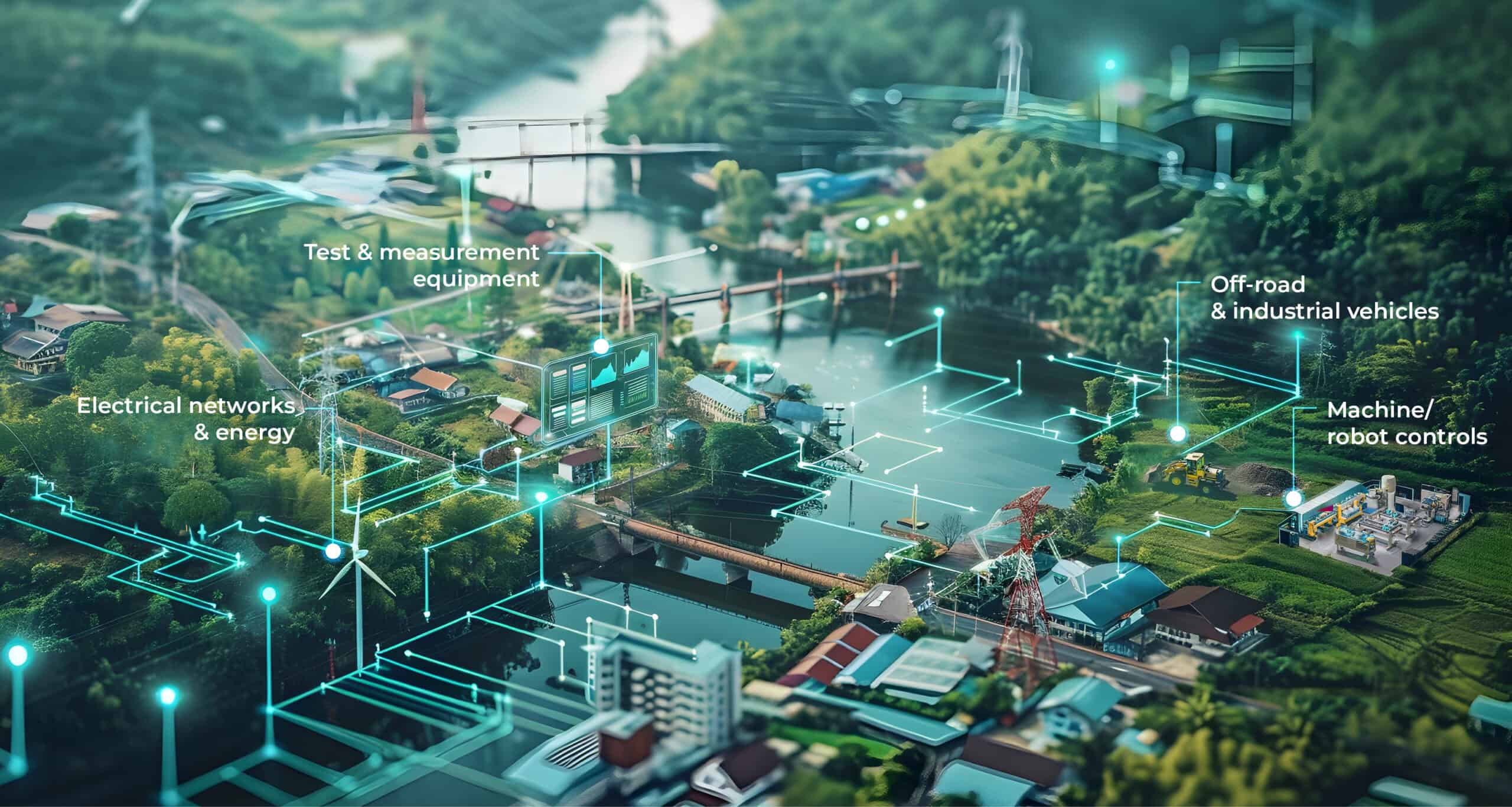
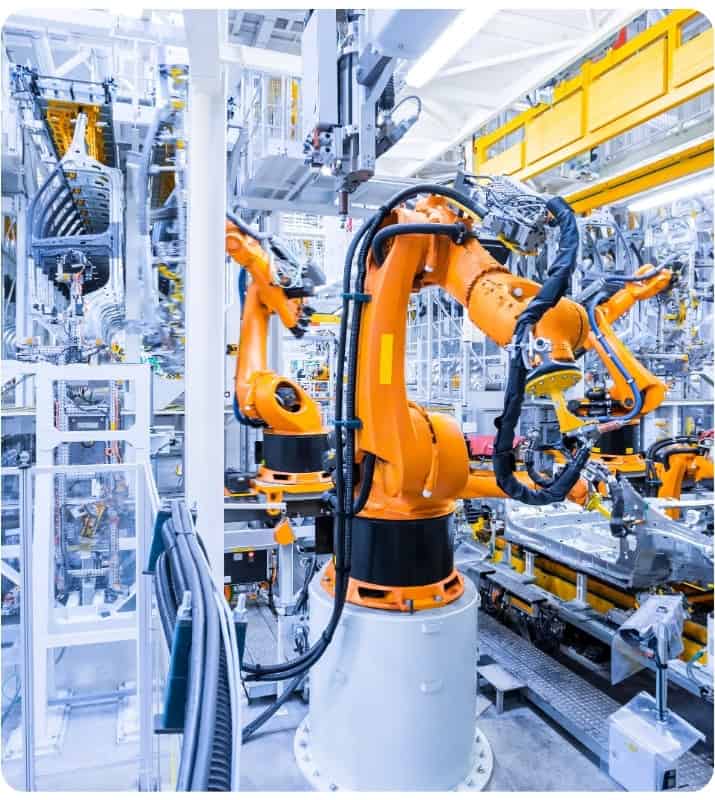
Machine / robot controls
Advanced control and supervision solutions to maximize operational efficiency:
- Industrial automation systems
- Programmable logic controllers (PLCs)
- Motion controllers
- Embedded systems for industrial and collaborative robots
- Human-machine interfaces (HMIs).
Test & measurement equipment
Precise systems for real-time monitoring and analysis of industrial performance:
- Oscilloscopes
- Spectrum analyzers
- Digital multimeters
- Smart sensors & interfaces
- Test benches used for the validation of electronic components and systems
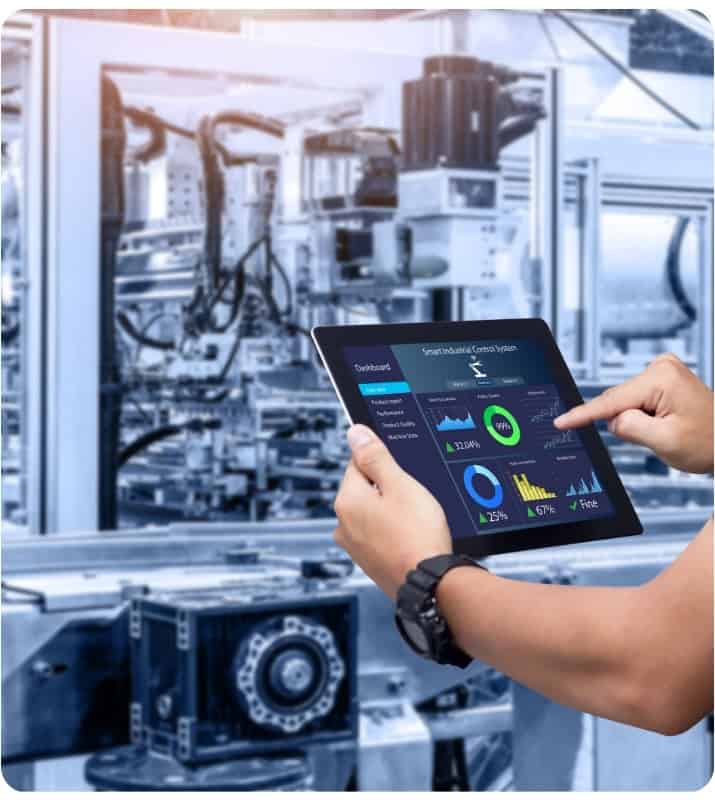
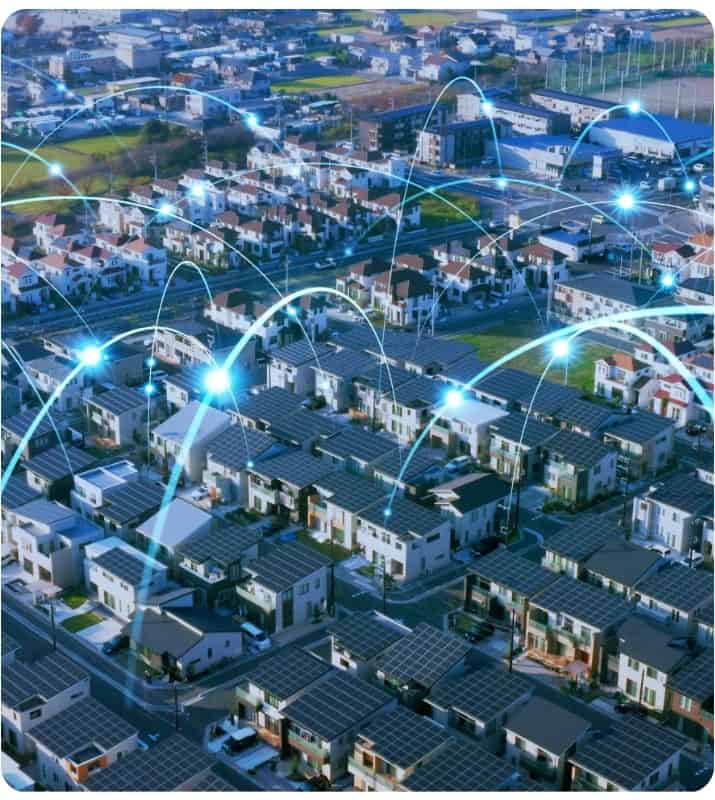
Electrical networks and energy storage
Innovative technologies for smart grids and energy efficiency:
- Inverters
- Battery management systems (BMS)
- Power converters
- Electrical network supervisors
- Charging stations for electric vehicles.
Off-road and
industrial vehicles
Robust electronic solutions for automation and industrial performance:
- Engine control systems
- Onboard computers
- Telemetry sensors
- Transmission control units
- Hydraulic and electronic management systems for industrial and agricultural machinery.
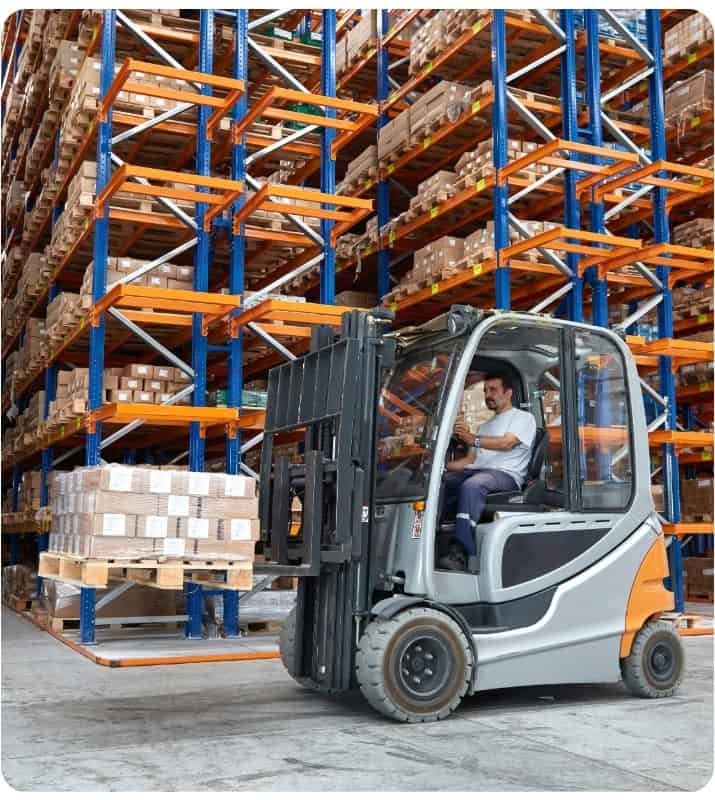
IIoT: developing your industrial connected objects
In a world where industrial IoT is redefining production chains, we offer cutting-edge expertise to support your transformation.
Whether you’re a novice or an expert in electronics, our team will guide you from design to final industrialization of your connected products.
- Customized design: our services cover the entire lifecycle, from specification to optimization of an existing product.
- Functional redesign: we help you reduce costs while adding key functionalities to enhance the competitiveness of your industrial solutions.
Our IIoT solutions satnd out by their ability to transform complex infrastructures into intelligent connected networks, meeting your industry’s present and future needs.
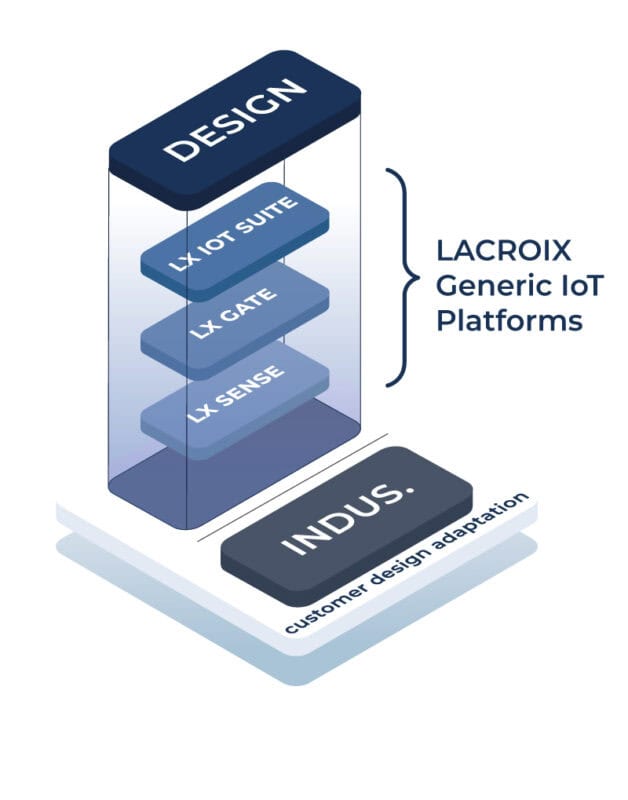
Platforms to accelerate development
We have designed three generic and customizable platforms to optimize your projects:
- LX SENSE: Sensor solutions
- LX GATE: Gateway solutions
- LX IoT Suite: IoT platform modules
These platforms help reduce costs, accelerate development, and ensure a high level of cybersecurity.
Our certifications
LACROIX is a contributing member of the IPC, and its teams work to IPC standards. In addition, CIT and CIS IPC-A-610 and CIS IPC-7711/7721 certified staff are available on each site. We are also UL ZPV12, ZPV18 certified
Our production plants dedicated to the Industry
You have a project
for an industrial
electronics product ?
Talk to our experts to discover how our electronics and industrial IoT solutions can transform your business. We help optimize operations, improve efficiency, and integrate smart solutions tailored to your specific challenges.
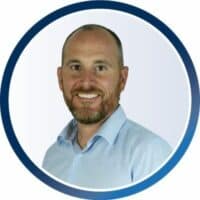
Alban-Thomas Béduneau
Sales Director EMEA Industrial / Avionics & Defence
Contact