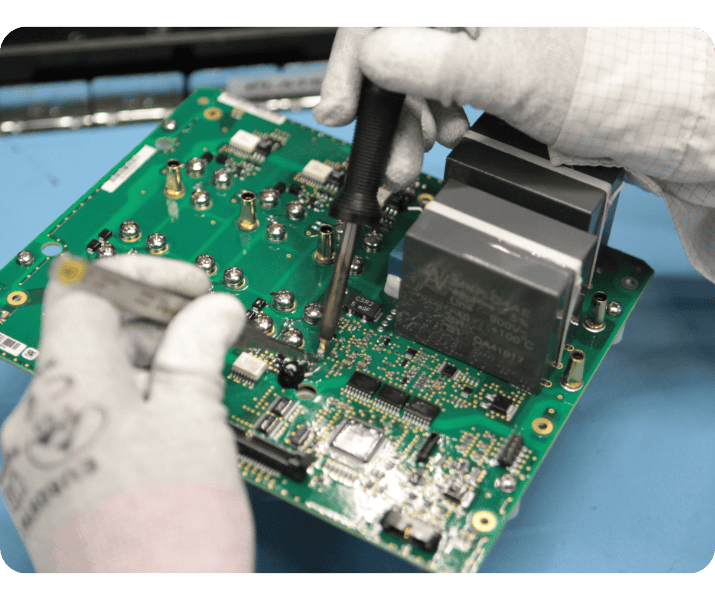
DfM: Optimizing Manufacturing from the Design Stage
Design for Manufacturing (DfM) ensures that your product is designed for efficient and defect-free production. By incorporating design guidelines, advanced assembly tools, and NPI analysis, we optimize the alignment between product design and industrial processes.
DfT: Ensuring Optimal Testability
Design for Testability (DfT) integrates a testing strategy from the early design phase to ensure product quality while controlling costs. Using tools like Test Expert, Testway, and testing solutions such as InSitu, Functional, and Boundary Scan, we ensure that each product can be efficiently and reliably tested.
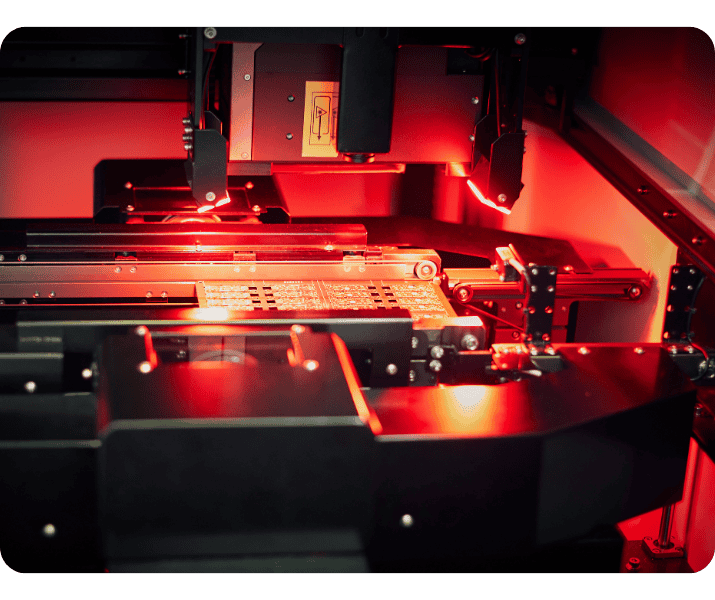
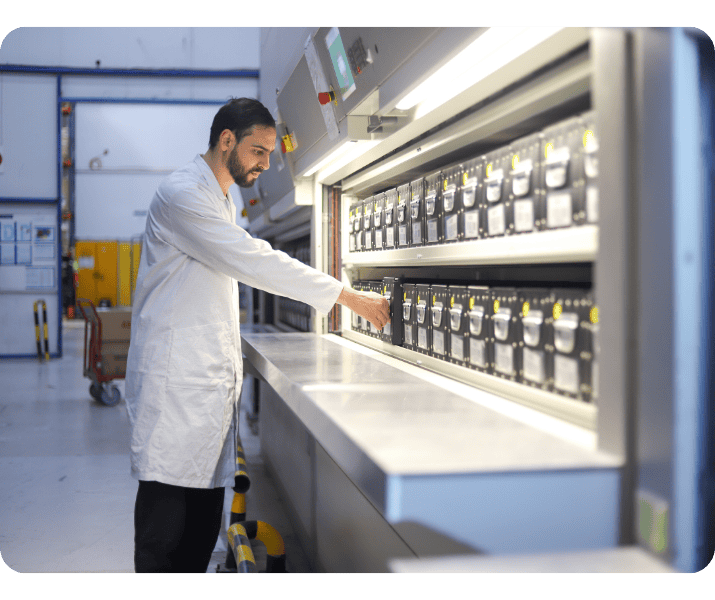
DfP: Securing Procurement and Component Sustainability
Design for Procurement (DfP) focuses on anticipating and optimizing the supply chain. Our experts select the most suitable components and suppliers early in the project lifecycle, considering cost, lead times, sustainability, and obsolescence risks. We leverage tools such as Z2DATA and our extensive supplier network to secure your supply chain.
Design For Excellence: Tailored Support for a Successful Industrialization
Our experts support you throughout your product’s lifecycle with customized services, including:
- Analysis of input data to identify improvement opportunities
- Detailed DfX reports with specific recommendations
- Close collaboration between our R&D and Industry 4.0 production teams to ensure industrial success
Accelerate your development with Design for Excellence
Leverage our advanced expertise in design and industrialization with our DfX approach. Reduce your time-to-market, optimize costs, and ensure product quality from the design stage.